Vlastnosti výroby drevených betónových blokov vlastnými rukami
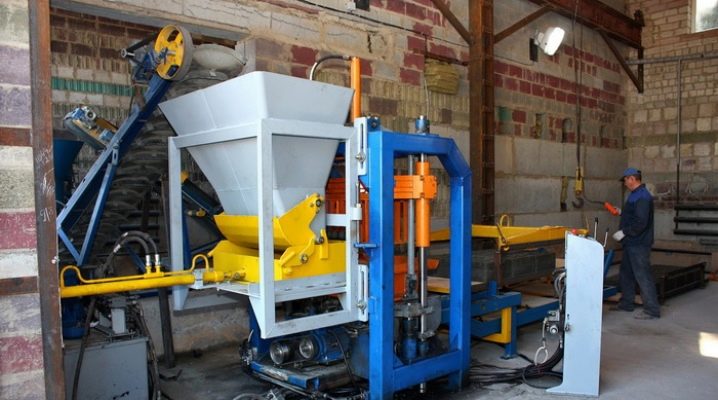
Arbolit je s nadšením opísaný v mnohých publikáciách, inzerenti sa neunúvajú pripisovať mu rôzne výhody. Ale aj keď odhliadneme od marketingových trikov, je jasné, že tento materiál si zaslúži dôkladnú kontrolu. Je dobré vedieť, ako na to sám.
Typy a veľkosti blokov
Arbolitové panely sú rozdelené do niekoľkých typov:
- veľkoformátové bloky (určené na murovanie hlavice stien);
- duté výrobky rôznych veľkostí;
- dosky na spevnenie tepelnej izolácie.
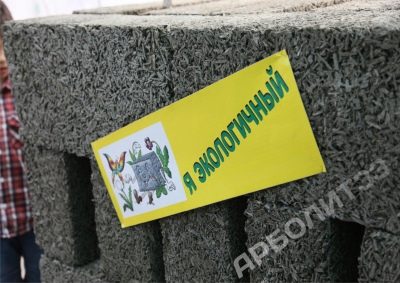
Tiež drevený betón sa používa na výrobu tekutých zmesí, s ktorou sa vylievajú uzatváracie konštrukcie. Najčastejšie sa však v praxi slovo „arbolit“ chápe ako murovacie prvky s obkladom alebo bez neho. Najčastejšie sa vyrábajú bloky s rozmermi 50x30x20 cm.Nomenklatúra sa však čoraz viac rozširuje a výrobcovia si osvojujú nové pozície. Technické vlastnosti vyrobených blokov sú poskytované iba pri úplnej absencii nečistôt.
Prvky s hustotou 500 kg na 1 cu. m a viac sa tradične považujú za štrukturálne, menej husté - určené na tepelnú izoláciu. Môžu sa použiť tam, kde zaťaženie zhora preberajú iné časti konštrukcie. Zvyčajne sa hustota meria až potom, čo blok stratil všetku prebytočnú vlhkosť.
Z liateho dreveného betónu so špecifickou hmotnosťou 300 kg na 1 cu. možno postaviť aj steny, pričom z hľadiska pevnosti nie sú horšie ako konštrukcie z ťažšieho materiálu.
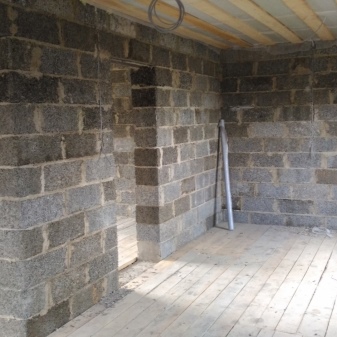
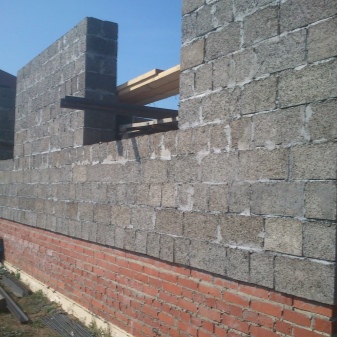
Stavať nosiče steny jednoposchodových domov, ktorých výška nepresahuje 3 m, je potrebné použiť tvárnice minimálne kategórie B 1,0... Ak sú štruktúry vyššie sú povinné produkty kategórie 1.5 a vyššie. Dvojpodlažné a trojpodlažné budovy by však mali byť postavené z drevobetónu skupiny B 2.0 alebo B 2.5.
Podľa ruskej GOST by mali mať drevené betónové konštrukcie v miernom klimatickom pásme hrúbku 38 cm.
V skutočnosti sú steny obytných budov z blokov 50x30x20 cm usporiadané v jednom rade, striktne ploché. Ak je potrebné vytvoriť pomocnú tepelnú izoláciu, z drevobetónu sa vyrába takzvaný teplý omietkový systém... Pripravuje sa pridaním perlitu a vytvorením vrstvy 1,5 až 2 cm.
Keď priestory nie sú vykurované alebo sú z času na čas vykurované, použite metódu muriva na okraji. Tepelne tienenie drevobetónových tvárnic má koeficient absorpcie vody maximálne 85%. Pre konštrukčné prvky je prípustná hodnota o 10 % nižšia.
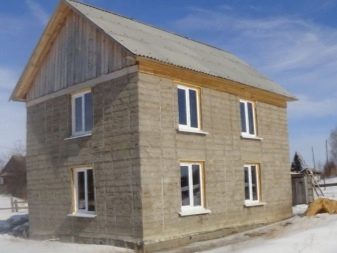
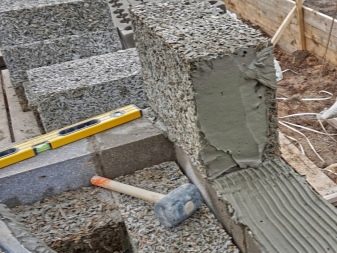
Drevobetónové bloky je obvyklé rozdeliť do troch kategórií podľa požiarnej ochrany:
- D1 (ťažko sa zapáliť);
- V 1 (veľmi horľavý);
- D1 (prvky s nízkou dymivosťou).
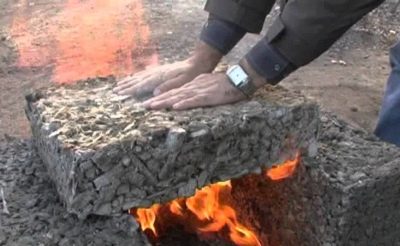
Potreba vyrábať drevený betón doma je do značnej miery spôsobená skutočnosťou, že existujúci výrobcovia často vyrábajú nekvalitný tovar. Problémy môžu súvisieť najmä s nedostatočnou pevnosťou, slabou odolnosťou proti prestupu tepla alebo porušením geometrických parametrov. Bloky akéhokoľvek druhu by mali byť určite pokryté omietkou.... Spoľahlivo chráni pred fúkaním vetra. S dreveným betónom sa kombinujú iba dokončovacie nátery schopné "dýchať"..
Existuje 6 značiek drevených betónových blokov, ktoré sa vyznačujú úrovňou mrazuvzdornosti (od M5 do M50). Číslo za písmenom M ukazuje, koľko cyklov prechodu cez nula stupňov môžu tieto bloky preniesť.
Minimálna mrazuvzdornosť znamená, že výrobky by sa mali používať iba na vnútorné priečky.
Ich veľkosť je najčastejšie 40x20x30 cm.V závislosti od zariadenia drážkovo-hrebeňového systému závisí plocha muriva a tepelná vodivosť stien.
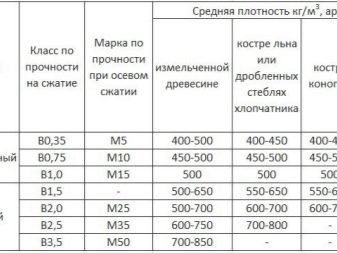
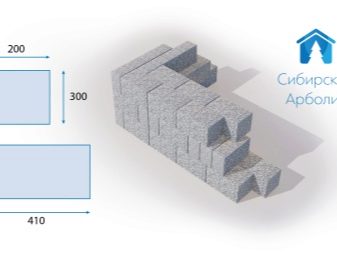
Keď už hovoríme o rozmeroch a vlastnostiach drevených betónových blokov v súlade s GOST, nemožno len povedať, že prísne reguluje maximálne odchýlky rozmerov. takže, dĺžka všetkých rebier sa môže líšiť od deklarovaných ukazovateľov nie viac ako 0,5 cm... Najväčší rozdiel uhlopriečok je 1 cm. A porušenie priamosti profilov každého povrchu by nemalo byť väčšie ako 0,3 cm... Čím vyššia je štruktúra, tým menej švov bude počas inštalácie a tým menší bude počet švíkov.
V niektorých prípadoch sú najvýhodnejšie tvárnice s rozmerom 60x30x20 cm, sú potrebné tam, kde je dĺžka stien násobkom 60 cm, odpadá tak rezanie tvárnic.
Niekedy sa vyskytuje takzvaný „severný arbolit“, ktorého dĺžka nepresahuje 41 cm. V niektorých radoch sa pri obväzovaní zhoduje šírka steny s dĺžkou kvádra, v druhej časti je súčet dvoch šírok a švu, ktorý ich oddeľuje.
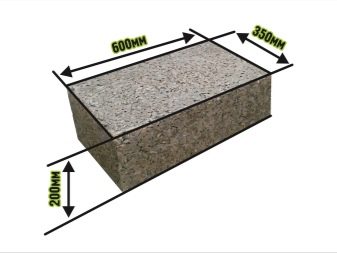
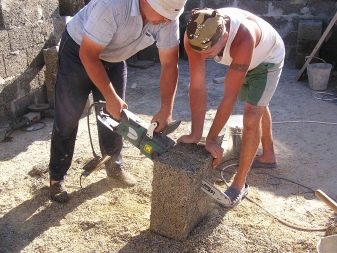
Takmer všetci výrobcovia vyrábajú usmerňovacie bloky. V rade každej spoločnosti je veľkosť takýchto výrobkov 50% štandardnej veľkosti. Príležitostne sa nájdu konštrukcie s rozmermi 50 x 37 x 20 cm, čo vám umožní postaviť steny presne 37 cm bez použitia obväzových blokov alebo použitia panelov.
V niektorých regiónoch sa môžu vyskytnúť úplne odlišné veľkosti, to by sa malo špecifikovať dodatočne. V prípade vlastnej výroby ich treba vybrať podľa vlastného uváženia.
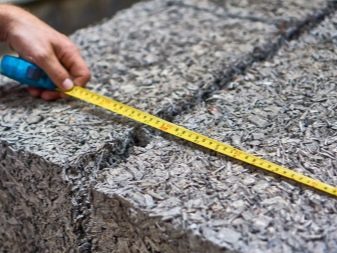
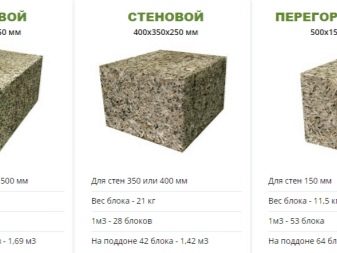
Zloženie a pomery zmesi
Pri príprave výroby drevobetónových panelov je potrebné starostlivo vybrať zloženie zmesi a pomer medzi jej časťami. Odpad zo spracovania dreva vždy pôsobí ako plnivo. Ale keďže drevený betón je typ betónu, obsahuje cement.
Vďaka organickým zložkám materiál dokonale udržuje teplo a neumožňuje prenikaniu cudzích zvukov. Ak však dôjde k porušeniu základných proporcií, dôjde k porušeniu týchto vlastností.
Malo by byť zrejmé, že na výrobu dreveného betónu možno použiť iba niektoré typy hoblín. To je jeho podstatný rozdiel od pilinového betónu. Podľa súčasnej GOST sú rozmery a geometrické charakteristiky všetkých frakcií materiálu prísne regulované.
Štiepky sa vyrábajú drvením nepredajného dreva. Dĺžka čipov sa pohybuje od 1,5 do 4 cm, ich maximálna šírka je 1 cm a hrúbka by nemala byť väčšia ako 0,2 - 0,3 cm.
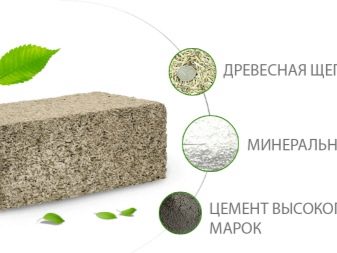
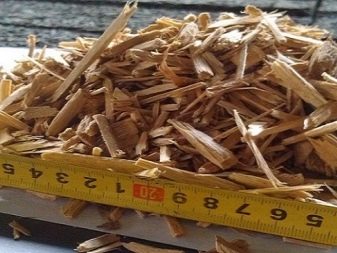
V dôsledku špeciálneho vedeckého a praktického výskumu sa zistilo, že najlepšie drevené štiepky:
- tvarom pripomína krajčírsku ihlu;
- má dĺžku až 2,5 cm;
- má šírku 0,5 až 1 a hrúbku 0,3 až 0,5 cm.
Dôvod je jednoduchý: drevo s rôznymi pomermi inak absorbuje vlhkosť. Dodržiavanie rozmerov odporúčaných výskumníkmi umožňuje vyrovnať rozdiel.
Okrem veľkosti treba starostlivo vyberať aj druhy dreva. Smrek a buk budú fungovať, ale smrekovec nebude fungovať. Môžete použiť drevo brezy a osiky.
Bez ohľadu na zvolené plemeno je nevyhnutné používať antiseptické zmesi.
Umožňujú vyhnúť sa výskytu plesňových hniezd alebo poškodeniu surovín inými patologickými hubami.
Pri výrobe drevobetónu sa niekedy používa kôra a ihličie, ale ich maximálny podiel je 10 a 5 %.
Niekedy berú aj:
- ľanový a konopný oheň;
- ryžová slama;
- bavlnené stonky.
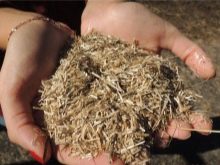
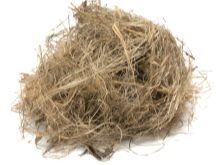
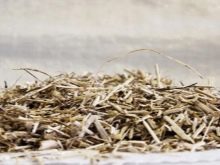
Najväčší dĺžka takýchto komponentov je maximálne 4 cm a šírka by nemala byť väčšia ako 0,2 - 0,5 cm. Je zakázané používať kúdeľ a ťažiť viac ako 5% hmotnosti použité plnivo. Ak sa používa ľanový oheň, bude musieť byť namočený vo vápennom mlieku na 24-48 hodín. Je to oveľa praktickejšie ako 3 alebo 4 mesiace vystavenia vonku. Ak sa neuchýlite k takémuto spracovaniu, cukor obsiahnutý v ľane zničí cement.
Čo sa týka samotného cementu, Na výrobu dreveného betónu sa najčastejšie používa portlandský cement... Práve on sa na tento účel začal využívať pred niekoľkými desaťročiami. Niekedy sa do portlandského cementu pridávajú pomocné látky, ktoré zvyšujú mrazuvzdornosť konštrukcií a zlepšujú ich ďalšie vlastnosti. V niektorých prípadoch sa môže použiť aj cement odolný voči síranom. Účinne odoláva účinkom množstva agresívnych látok.
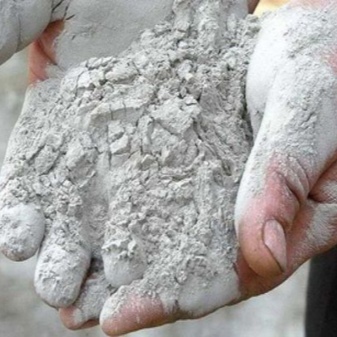
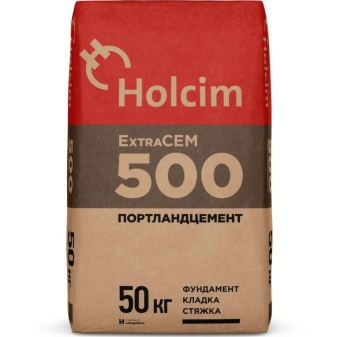
GOST vyžaduje, aby sa do tepelne izolačného dreveného betónu pridával iba cement triedy M-300 a vyšší. Pre konštrukčné bloky sa používa iba cement kategórie nie nižšej ako M-400. Pokiaľ ide o pomocné prísady, ich hmotnosť môže byť od 2 do 4% z celkovej hmotnosti cementu. Počet zavedených komponentov je určený značkou drevených betónových blokov. Chlorid vápenatý a síran hlinitý sa spotrebujú v objeme nie väčšom ako 4%.
To isté je limitné množstvo zmesi chloridu vápenatého so síranom sodným. Existuje tiež niekoľko kombinácií, v ktorých je chlorid hlinitý kombinovaný so síranom hlinitým a chloridom vápenatým. Tieto dve kompozície sa používajú v množstve do 2 % z celkovej hmotnosti ukladaného cementu. V každom prípade je pomer medzi pomocnými prísadami 1: 1... Aby však adstringentné zložky fungovali efektívne, musíte použiť vodu.
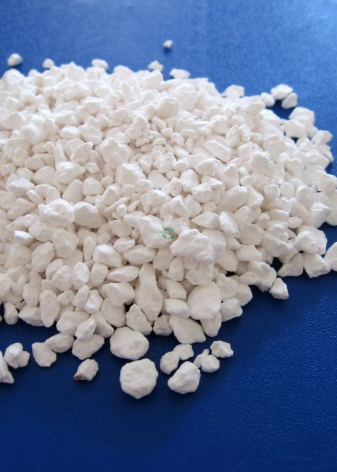
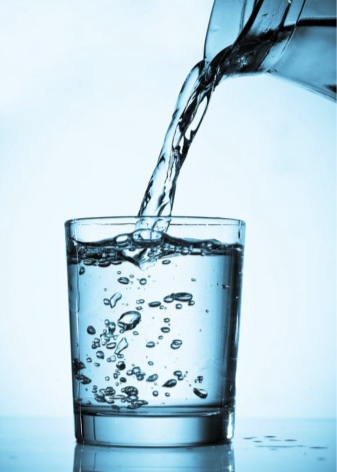
GOST predpisuje prísne požiadavky na čistotu použitej kvapaliny. Pri samotnej výrobe drevobetónu však často odoberajú akúkoľvek vodu, ktorá je vhodná pre technické potreby. Normálne tuhnutie cementu vyžaduje zahriatie až na +15 stupňov... Ak teplota vody klesne na 7-8 stupňov Celzia, chemické reakcie sú oveľa pomalšie. Pomer zložiek je zvolený tak, aby zabezpečil potrebnú pevnosť a hustotu dreveného betónu.
Arbolitové výrobky môžu byť vystužené oceľovými pletivami a tyčami. Hlavná vec je, že spĺňajú priemyselné normy.
Norma vyžaduje, aby výrobcovia testovali pripravenú zmes dvakrát za smenu alebo častejšie, či sú v súlade s nasledujúcimi ukazovateľmi:
- hustota;
- jednoduchosť stylingu;
- sklon k delaminácii;
- počet a veľkosť dutín oddeľujúcich zrná.
Testovanie sa vykonáva v špeciálnom laboratóriu. Vykonáva sa pre každú dávku zmesi 7 a 28 dní po vytvrdnutí. Mrazuvzdornosť sa musí určiť pre dekoratívne aj nosné vrstvy.
Aby zistili tepelnú vodivosť, merajú ju na vzorkách vybraných podľa špeciálneho algoritmu. Stanovenie vlhkosti sa vykonáva na vzorkách odobratých z hotových kamenných blokov.
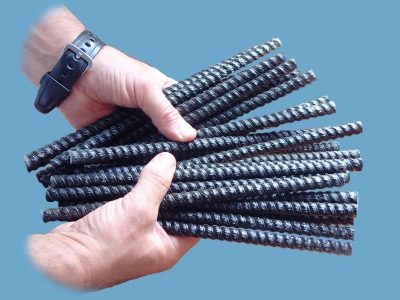
Potrebné vybavenie
Iba v prípade, že sú splnené všetky požiadavky GOST, je možné uviesť do výroby určitú značku dreveného betónu. Ale na zabezpečenie prísneho dodržiavania noriem a uvoľnenia požadovaného množstva zmesi a následného blokovania z nej pomáha iba špeciálne vybavenie. Štiepky sa delia na časti pomocou priemyselných brúsok. Ďalej spolu s ďalšími komponentmi vstupuje do zariadenia, ktoré mieša roztok.
Budete tiež potrebovať:
- Zariadenia na dávkovanie a tvarovanie drevených betónových blokov;
- vibračný stôl, ktorý im poskytne potrebné vlastnosti;
- zariadenia na sušenie triesok a varených blokov;
- bunkre, kde sa ukladá piesok a cement;
- linky dodávajúce suroviny.
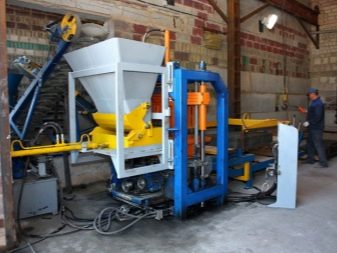
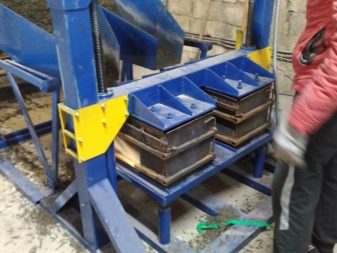
Ak plánujete vyrábať veľké dávky dreveného betónu, nemali by ste používať domáce zariadenia. Nie sú dostatočne produktívne, pretože ziskovosť podniku klesá.
Je užitočné zvážiť vlastnosti každého typu zariadenia. Zariadenia na rezanie triesok majú špeciálny bubon s "nožmi" vyrobený z vysoko kvalitnej nástrojovej ocele. Okrem toho je bubon vybavený kladivami, ktoré umožňujú automatizáciu dodávky surovín na následné drvenie.
Aby surovina prešla dovnútra, bubon je vyrobený perforovaný, je obklopený niekoľkými. Väčší (vonkajší) bubon rovnakého tvaru, ktorý zabraňuje rozhadzovaniu nečistôt.Zvyčajne je zariadenie namontované na rámoch s trojfázovými elektromotormi. Po rozštiepení sa triesky presunú do sušičky. Práve kvalita tohto zariadenia najviac ovplyvňuje dokonalosť hotového výrobku..
Sušička je vyrobená aj vo forme dvojitého bubna, jej priemer je približne 2 m.Vonkajší bubon je perforovaný, čo umožňuje prívod teplého vzduchu. Napája sa pomocou azbestovej rúry alebo flexibilnej ohňovzdornej hadice. Krútenie vnútorného bubna umožňuje štiepky premiešať a zabrániť vznieteniu suroviny. Kvalitné sušenie dokáže uviesť 90 alebo 100 blokov do požadovaného stavu za 8 hodín... Presná hodnota závisí nielen od jeho výkonu, ale aj od rozmerov spracovávaných štruktúr.
Miešadlo je veľká valcová vaňa. Všetky potrebné suroviny sa naložia zboku a namiešaná kompozícia vychádza zospodu. Elektromotory a ich prevodovky sú zvyčajne umiestnené na vrchnej časti miešačky malty. Tieto motory sú vybavené nožovými zostavami. Kapacita nádrže je určená dennou kapacitou linky. Miniatúrna výroba nevyrobí za dennú zmenu viac ako 1000 vzorov, pričom sa používajú kade s objemom 5 metrov kubických. m.
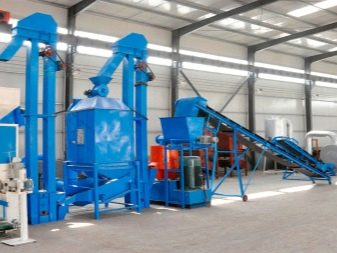
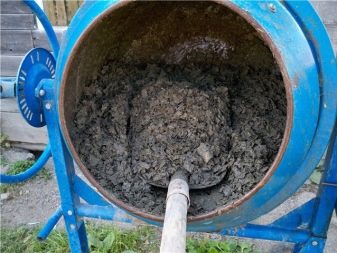
Technológia výroby
Na prípravu drevených betónových blokov pre súkromný dom vlastnými rukami musíte použiť 1 diel hoblín a 2 diely pilín (hoci v niektorých prípadoch je preferovaný pomer 1: 1). Toto všetko sa pravidelne suší. Vonku sa uchovávajú 3 až 4 mesiace. Periodicky nasekané drevo je ošetrené vápnom, prevrátené. Zvyčajne 1 kubický meter. m.štiepky spotrebujú asi 200 litrov vápna v koncentrácii 15%.
Ďalšia fáza výroby drevených betónových blokov doma zahŕňa miešanie drevených triesok s:
- portlandský cement;
- hasené vápno;
- chlorid draselný;
- tekuté sklo.
Bloky s rozmermi 25x25x50 cm je najlepšie vyrobiť doma.... Práve tieto rozmery sú optimálne pre bytovú aj priemyselnú výstavbu.
Zhutňovanie malty vyžaduje použitie vibračných lisov alebo ručných ubíjadiel. Ak nie je potrebný veľký počet dielov, možno použiť miniatúrny stroj. Špeciálne tvary pomáhajú nastaviť presnú veľkosť hotového výrobku.
Formovanie dosiek
Monolitický drevený betón môžete vyrobiť tak, že pripravenú zmes do tejto formy nalejete ručne. Ak sa pridá vodné sklo, hotový výrobok sa stane tvrdším, no zároveň sa zvýši jeho krehkosť. Odporúča sa miesiť komponenty postupne, a nie všetky dohromady. Potom je menšie nebezpečenstvo hrčiek. Získanie ľahkej konštrukcie je veľmi jednoduché - do formy stačí vložiť drevený blok.
Obrobok je potrebné udržiavať v tvare aspoň 24 hodín... Potom začne sušenie vzduchom pod prístreškom. Doba schnutia je určená teplotou vzduchu a ak je veľmi nízka, niekedy trvá aj 14 dní. A následná hydratácia pri 15 stupňoch vydrží 10 dní. V tomto štádiu je blok držaný pod fóliou.
Aby drevobetónová doska vydržala dlhšie, nemala by sa ochladiť na negatívnu teplotu. Drevený betón v horúcom letnom dni takmer nevyhnutne vysychá. Tomu sa však dá vyhnúť pravidelným postrekom vodou. Najbezpečnejšou metódou je spracovanie za plne kontrolovaných podmienok v sušiarni. Požadované parametre - ohrev do 40 stupňov s vlhkosťou vzduchu od 50 do 60%.
Informácie o tom, ako vyrobiť drevené betónové bloky vlastnými rukami, nájdete v nasledujúcom videu.
Komentár bol úspešne odoslaný.